In a world where every detail counts, the ability to design both internal and external threads tailored to your project can make all the difference. Whether you’re working with fine thread gauges, complex thread profiles, or specific metric or inch threads, 3D printing empowers you to add screw threads with confidence, knowing they will perform as intended.
How to incorporate threads into a 3D design?
Incorporating threads into a design has its set of challenges. Luckily, there are several ways to add threads to a 3D-printed part.
Printing Threads
One of the most effective ways to incorporate threads in a design is by printing them directly into the design. It allows flexibility in customization and delivers maximum flexibility.
However, directly printing smaller diameters is quite difficult, so it’s best to use this technique with threads bigger than 6mm or M6 screws.
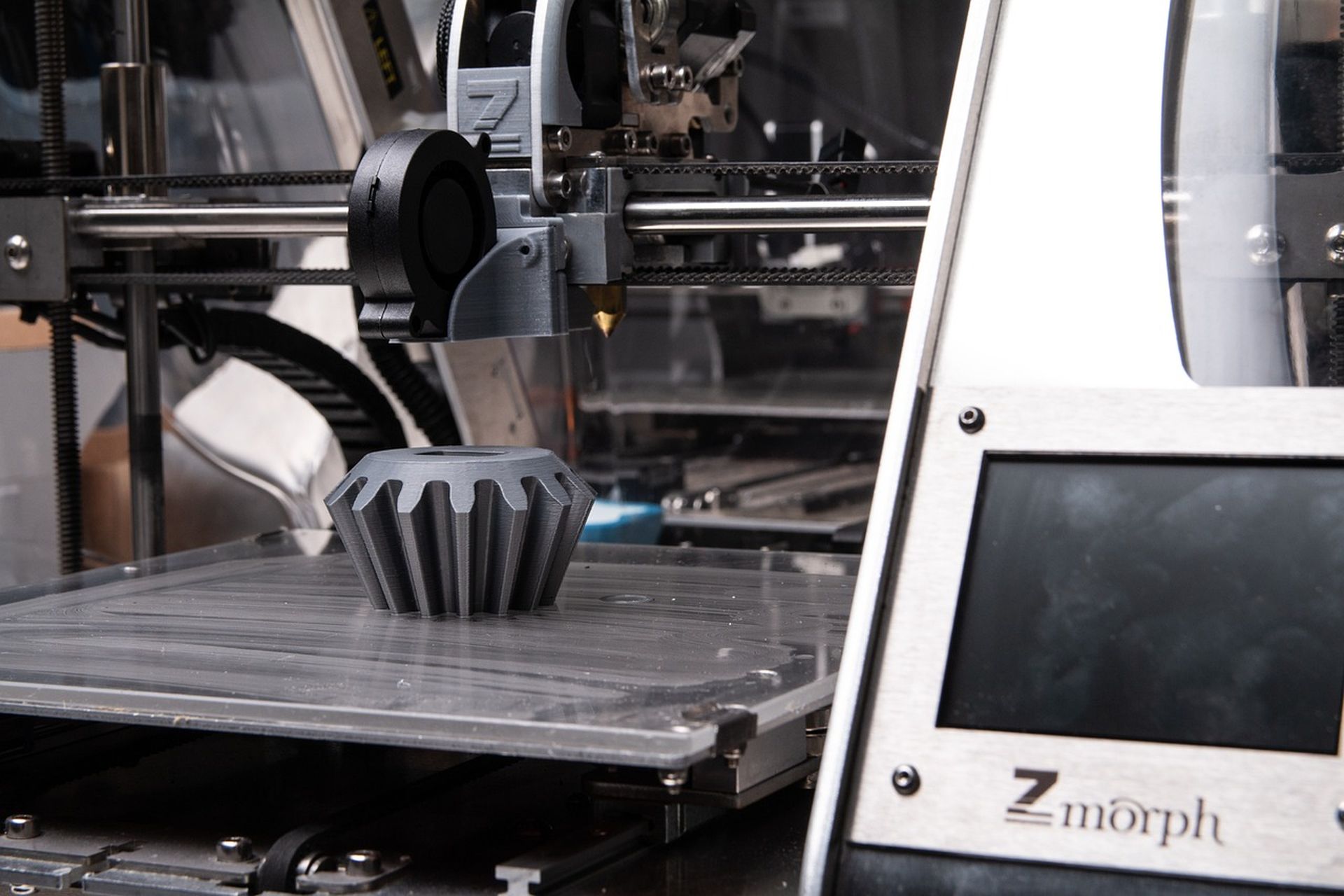
Also, remember that the threads can’t stand longer cycles of assembling as they are not strong enough to add or remove a screw.
Lastly, direct printing is not a viable solution for making multiple copies. In such cases, it’s best to have additional printers, but it makes for an additional cost.
Using Heat-set inserts
This technique is great because thermoplastic and thermoset materials are commonly used in 3D printing.
For thermoplastic parts, heat set inserts use the combination of heat and pressure to permanently incorporate the threads to a part. This process is time-consuming as it requires the part to cool down, but it’s very simple and easy.
Using heat-set inserts for thermoset parts requires additional holding with glue. This process has also a high lead time as the glue needs to cure before the installation of the screw.
Manually drilling and tapping
This technique is probably the quickest and most economical way of incorporating threads into a 3D-printed design. The equipment needed for this process is easily accessible to everyone. However, the hold of the threads may not be as durable. The entire process is also quite time-consuming.
Combination of multiple methods
Using a combination of techniques may turn out to be the most effective way to incorporate threads. Incorporating 3D printed threads in areas with limited accessibility, along with using the combination of the above methods, can provide the best results. However, the lead time will be significant, as these methods typically require substantial processing time.
What are 3D-printed threads?
3D printed threads are helical grooves created through 3D printing technology, designed to work similarly to traditional screw threads used in fastening and mechanical systems. However, threads are not limited to screws; they are also found on pipes, linear drives, worm gears, and other devices.
The structure of threads has various features that define their shape, functionality, and compatibility with mating components. Here are the main elements of thread structure:
- Helical Path: Threads follow a helical path around the cylindrical surface, which can be internal or external.
- Thread Profile: The profile or cross-sectional shape of the thread can be triangular (V-thread), square, trapezoidal (Acme), and rounded.
- Pitch: The distance between corresponding points on adjacent threads.
- Root: This is the bottom of the surface of the thread running around the thread body
- Crest: This is the highest point of the thread profile.
- Major Diameter: The largest diameter of the thread, also known as nominal diameter.
- Minor Diameter: The smallest diameter of the thread.
- Pitch Diameter: The diameter at which the thread thickness is equal to the space between threads.
- Thread angle: The angle between the flanks of the thread, which connect the crest to the root.
3D-printed thread regulations
All commercial screws are standardized. Therefore when you model a threaded element it should be based on a standard. This makes your model more adaptable to commercially available parts.
Regulations distinguish between metric threads and inch threads, with metric used across the world in Europe, UK and Asia, while imperial are predominantly used in the USA.
Inch threads and their standard thread sizes are named with numbers which can be found in the Unified Thread Standard (UTS). The size is determined by major or minor diameter and the threads per inch (TPI).
Therefore, when you want to design threaded elements, you should get the specifications of pitch, angle, and all the rest from the recommended standard tables.
Metric threads are designated with the letter “M” and a number that stands for the nominal outer diameter of a thread in millimeters. For example, the M6 thread has a nominal outer diameter of 6 mm.
For external threads, the nominal outer diameter is equivalent to the major diameter. The nominal outer diameter of an internal thread can be determined by measuring the minor diameter and examining a metric thread table.
Metric thread chart
A metric thread chart is a reference tool that provides detailed information about metric screw threads, commonly used in engineering and manufacturing. The chart includes various parameters such as major and minor diameters, thread pitch, and pitch diameter that define the dimensions and tolerances of the threads.
These parameters and ISO metric thread profiles ensure compatibility and reliability in a wide range of applications. ISO metric thread profiles refer to the standardized thread profiles defined by the International Organization for Standardization (ISO) for use in screw threads.
Here are the key elements typically found in a metric thread chart:
- Thread size
- Pitch
- Major diameter
- Minor diameter
- Pitch diameter
- Tap drill size
Tap drill size refers to the difference between nominal diameter (major diameter) and thread pitch. Tap drill size allows the creation of a hole that allows the tap to cut threads into the material efficiently without causing excessive stress or damage to the tap or the workpiece.
To properly read a metric thread chart you need a thorough understanding of all the above measurements. This allows you to make a choice between coarse and fine threads. This will depend on application requirements, with coarse threads being suitable for quick assembly and rough environments, and fine threads offering higher precision and strength.
Advantages of 3D Printed Threads
3D printing threads offer multiple advantages as opposed to using off-the-shelf screws. The benefit of 3D printing threads is its exceptional adaptability and precision. This process meets specific threading requirements with accuracy and enhances manufacturing efficiency.
Let’s go over the most prominent benefits of 3d printed threads:
Streamlined prototyping and production
Using 3D-printed threads reduces turnaround time because it allows the integration of the threads directly into the 3D-printed part. This eliminates the need for post-printing operations such as drilling and tapping, speeding up production. As a result, you can quickly prototype and test threaded components, making it easier to iterate on designs and improve them.
Accessibility
Threads can be printed in locations that are challenging to reach with conventional tools, such as internal cavities or intricate parts. 3D printing allows you to add threads in places that would be difficult to drill and tap after print.Strength and Integrity
Threads printed as part of the component are often stronger and better aligned than those added afterward. Because there’s no need for drilling into the print afterward to install your threads you can use less infill percentage in your prints. This results in improved load distribution and reduced risk of misalignment or failure.
Providing precision
With 3D printing, thread geometry can be easily modified to achieve precise fits and functions. 3D printing can produce intricate thread shapes that might be impossible to achieve with traditional machining or casting methods.
Cost-efficiency
3D-printed threads are also a cost-effective option, especially for small-scale setups. The manufacturing process reduces material waste from drilling or tapping. It also eliminates the need for specialized tools and equipment for threading.
Design guide for 3D printing threads
Choosing suitable CAD software is crucial in designing threads for 3D printing. Your selection must match your design needs, the specific types of threads you plan to create, and the compatibility with the file formats used in 3D printing.
To design 3D printed threads you have two options. You can either use a toolbox your CAD software is equipped with or model it from scratch.
Usually, it’s not necessary to design a part from scratch. Most CAD software contains toolboxes of standard parts. So, chances are you won’t have to design a model using an existing commercially available part.
However, there are instances where you have to model threads from scratch. In such a case, you need to use a modelling tool in the CAD program. With an understanding of the basics of thread printing, it’s easy to manipulate models and input values to generate the desired threads.
It’s also crucial to consider the material you’ll use for printing. It will determine the durability and effectiveness of the part.
One of the most popular materials used for 3D printing is PLA because it’s easy to print with, however, it may not be as durable or heat-resistant as other materials.
ABS, on the other hand, is a durable, impact-resistant material. It’s suitable for functional prototypes and parts requiring mechanical strength. However, ABS can be more difficult to print with and requires a heated build platform.
You can also use metal 3D printing with aluminum or stainless steel. It allows high strength, durability, and precision. It is suitable for producing functional metal parts with complex geometries, especially threaded components.
3D printing process
Before printing threaded elements there are a few crucial printer setup steps to complete. Ensure your printer is properly calibrated, including the extruder calibration. Additionally, it’s highly recommended to level your print bed.
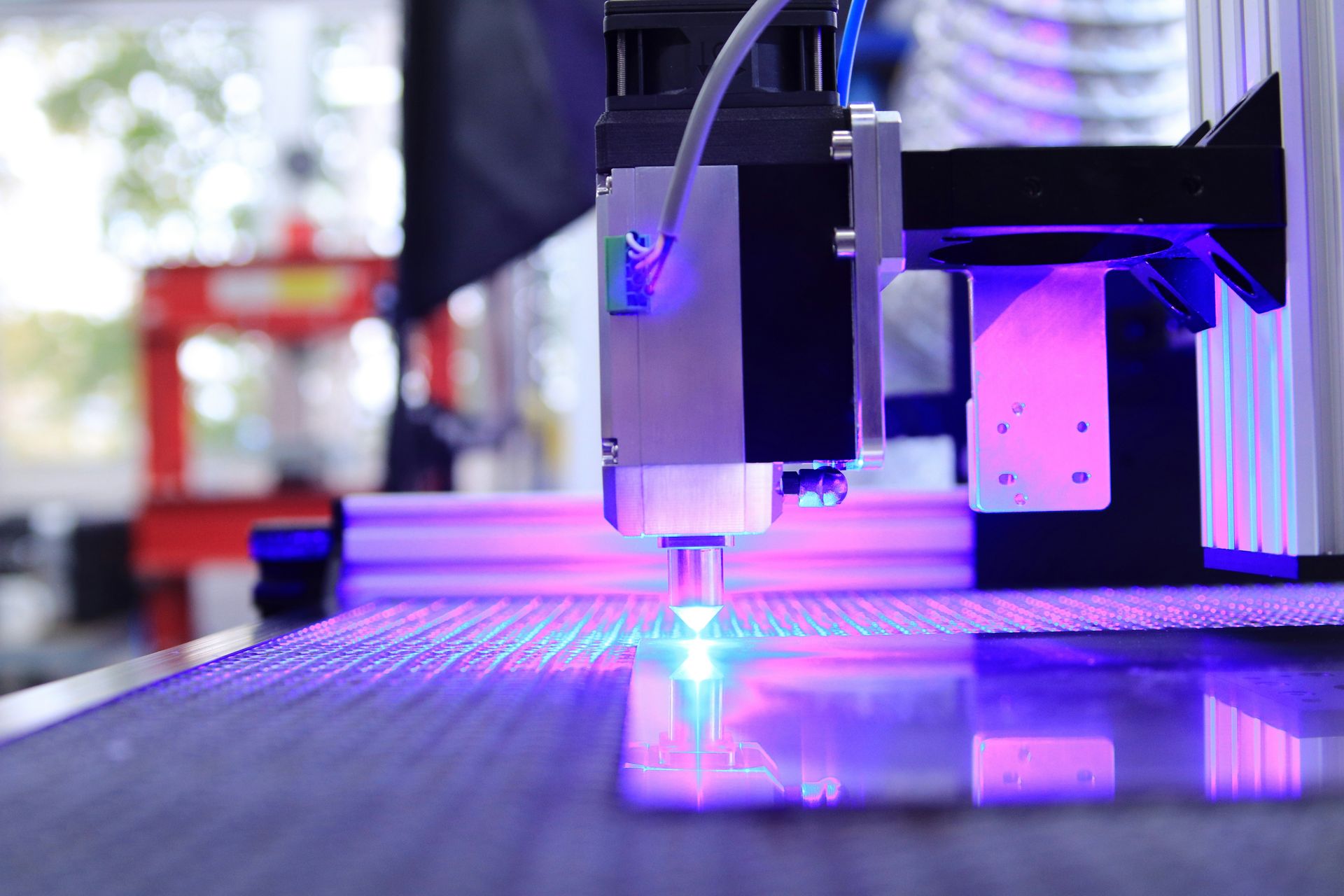
Depending on the purpose of your print, you should choose to print your threads vertically or horizontally. Printing threads vertically requires fewer supports and less post-processing but horizontal orientation allows for greater strength.
Try printing without any supports, especially the ones that go inside the thread. It may be difficult to remove them and sustain the proper performance, especially when it comes to internal threads.
To ensure that the printed thread is durable, use at least four vertical layers. Layer height is also a crucial parameter you should consider when printing threads. For smooth operation, the layers should be as thin as possible. As a guideline, threads larger than M12 or 1/2″ can be successfully printed with 0.2-mm layers, while smaller threads require thinner layers.
Also, it’s important to tweak infill density and ensure there is enough clearance between threads for them to fit together properly.
To enhance the durability and functionality of your threads, consider an infill density of at least 25%, maintaining a clearance of 0.15-2 mm between mating threads. Also, opting for thread profiles suited for plastics is a critical design consideration.
After printing your prototype, check if your threads fit and function as intended. Adjust your design as needed based on these tests.
Real-world applications of 3D printed threads
The significance of 3D-printed threads is apparent in their widespread use across multiple sectors. From the field of aerospace to the automotive industry and the healthcare sector, these threads play a crucial role in contemporary manufacturing processes.
Prototyping and product development
3D printed threads can accelerate prototyping, enabling rapid iteration and adaptation. It significantly reduces the time and cost associated with more labor-intensive traditional prototyping methods.
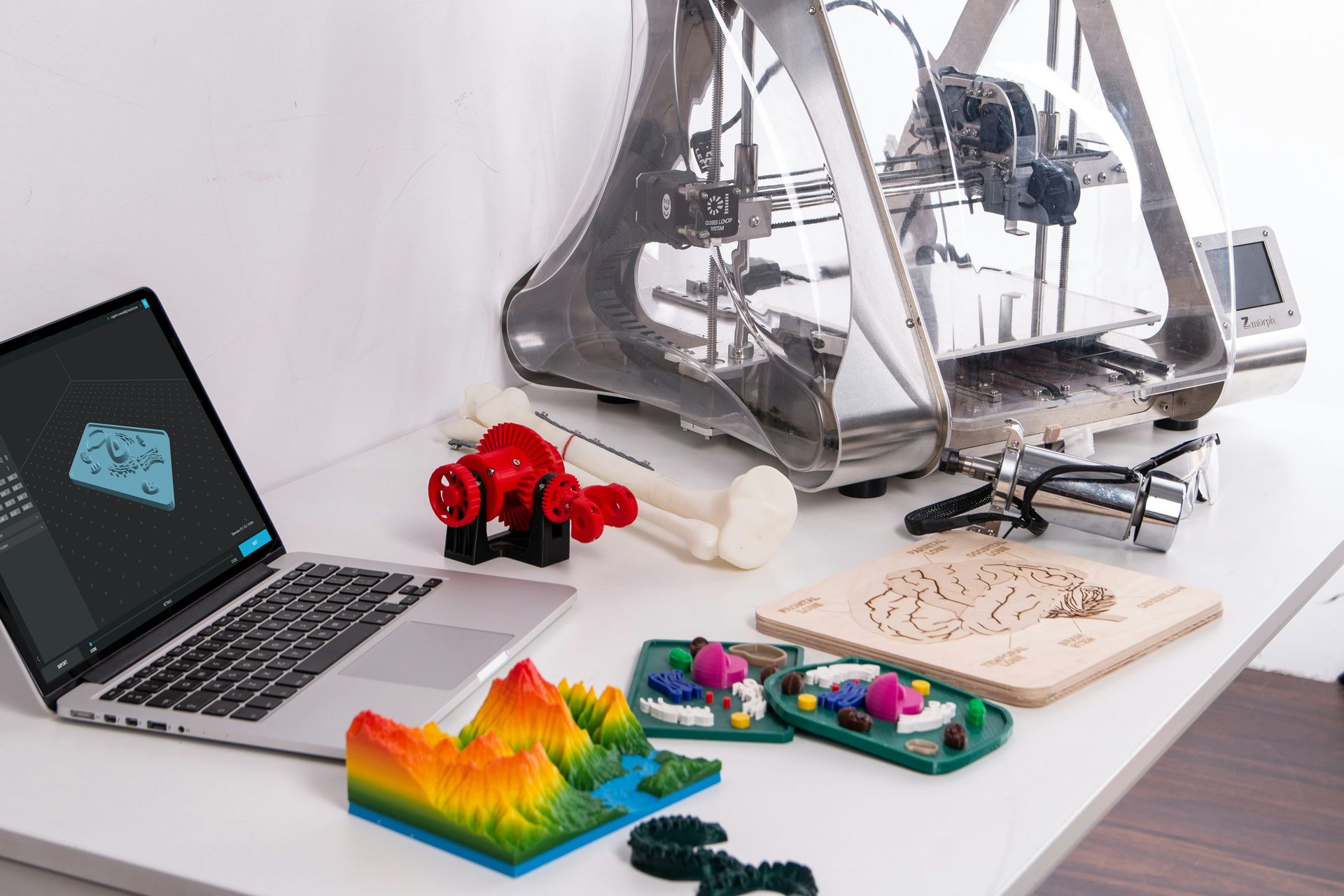
Custom fixtures and tools
Custom fixtures and tools benefit from the precision of 3D printed threads, enhancing workflow efficiency and task accuracy. This precision allows the creation of highly customized and intricate designs tailored to specific tasks or machinery.
End-use components
3D-printed threads can facilitate low-volume production, offering cost savings and design freedom. They are key to combining parts into cohesive products and streamlining design and assembly.
Conclusion
Mastering the creation of 3D-printed threads involves attention to detail in several key areas. It is essential to choose the correct thread dimensions and printing orientation, select the most suitable materials, and understand the different methods for incorporating threads into designs. Whether opting for direct printing, heat-set inserts, or manual techniques, each approach serves specific needs. Applying the right post-processing methods can further enhance the quality and durability of the final product. Focusing on these aspects allows leveraging 3D printing to create precise, efficient, and effective threaded components for various applications.
Featured image credit: Eray Eliaçık/Bing