The shipping industry moves over 11 billion tons worth of goods every year. With the growth of global trade and “just-in-time” deliveries, the pressures on shippers to deliver freight quickly, reliably, and cost-effectively have skyrocketed – and many are finding it hard to keep up. From intricate networks of full container load (FCL) shipping to smaller, consolidated shipments (LCL), each mode faces unique challenges.
Traditionally, shipping logistics have relied heavily on paper trails, phone calls to track containers down, and lots of manual work. Now, the game is changing with real-time tracking sensors and smart algorithms (backed by AI and machine learning) that optimize logistics on the fly. These technologies are bringing some much-needed visibility and efficiency into the complex world of shipping.
As such, the days of shippers losing their containers on long, complex journeys and scrambling to find them are quickly becoming a thing of the past. Modern logistics beats by the pulse of real-time tracking sensors, predictive algorithms, and end-to-end visibility platforms. Let’s explore how companies now monitor the exact location and status of containers from factory to port.
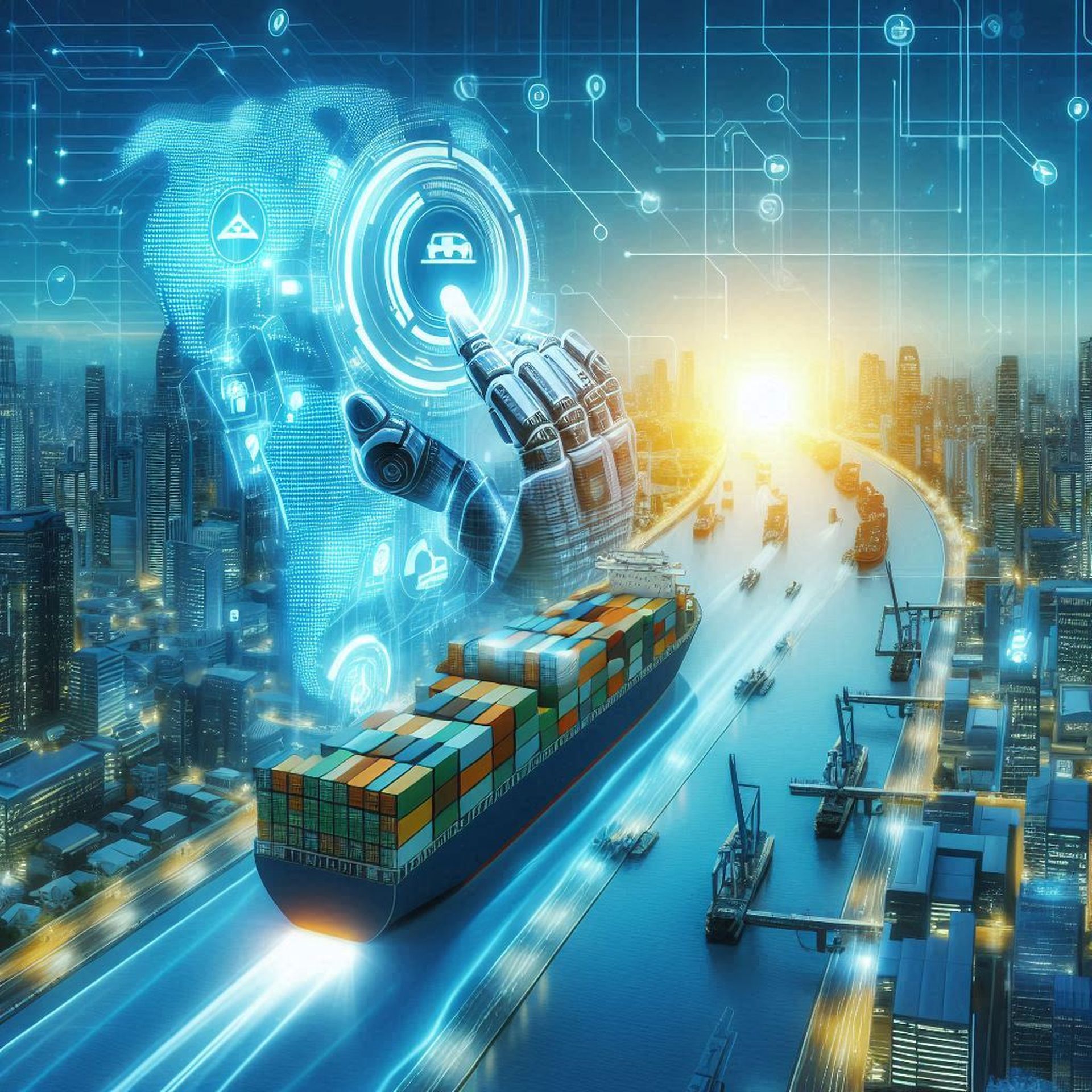
Why legacy shipping logistics can no longer keep up
As we just mentioned, old school freight shipping involved a lot of manual paperwork, phone calls, faxes, and tracking things down – what we might call “analog logistics.” Once a container left the shipper’s dock, they often lacked real-time visibility into its status and location during transit.
The hand-offs between ports, ships, trains and trucks were prone to delays and miscommunications. Containers could sit at ports waiting to be loaded or unloaded from vessels. Customs inspections and paperwork could also introduce long delays.
As such, most tracking was done retroactively. If a customer asked where their order was, the shipper would have to make lots of calls to find out. The carriers worked in silos, and there was little data sharing between them.
This uncertainty made it very difficult to anticipate delays or make contingency plans. As a result, shippers struggled to meet customer expectations around order accuracy and on-time delivery.
Sensors provide real-time container tracking
Businesses can now install inexpensive wireless sensors and GPS trackers directly onto shipping containers and chassis to track locations and status in real time. These handy devices beam information to the cloud through cell or satellite networks.
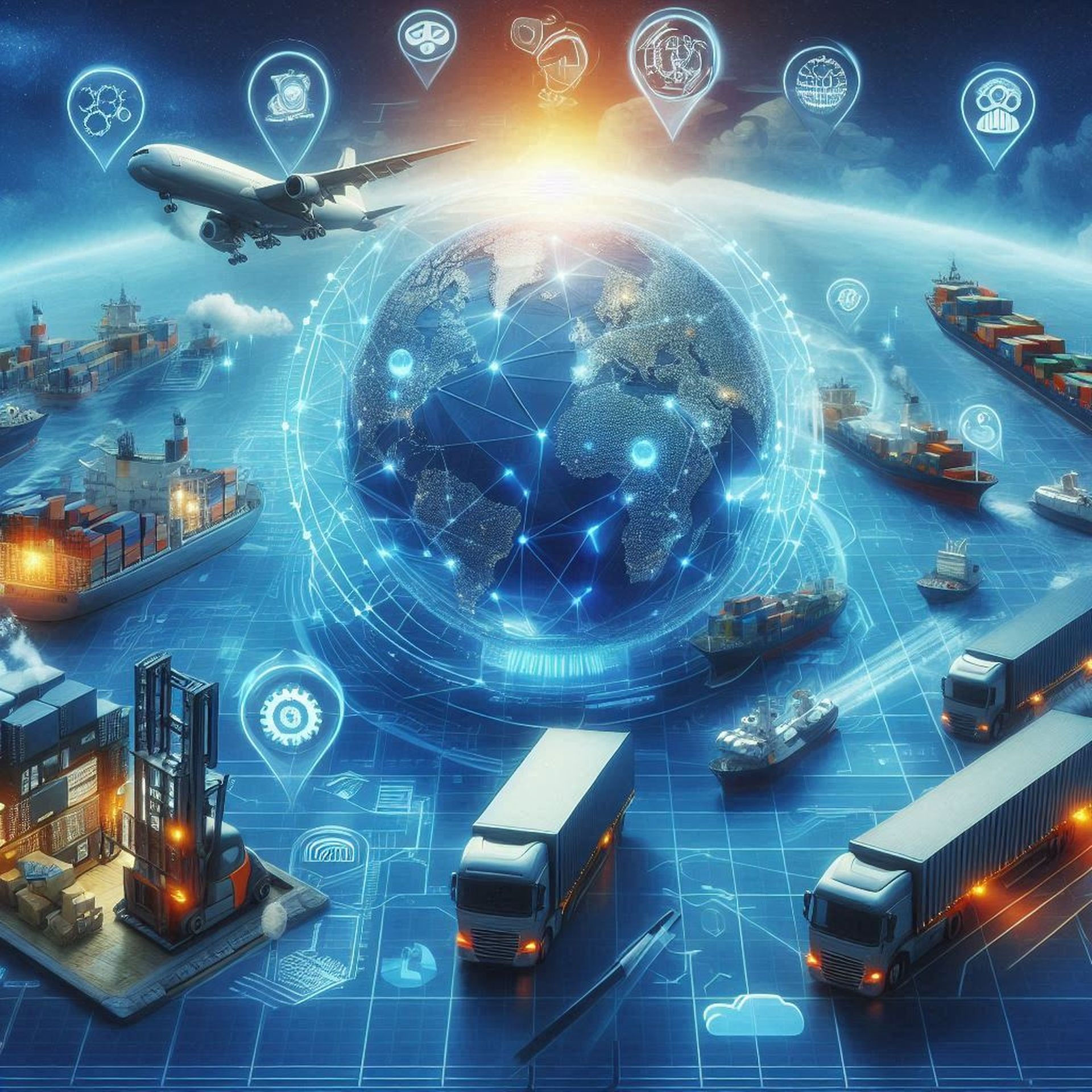
The tech has been especially beneficial for companies that rely on FCL shipping since it lets them see exactly where their containers are and what shape they’re in at any given moment. This means business owners rest easier knowing their precious cargo is safe, observing when a container reaches key milestones like vessel loading, port arrival, customs clearance, and so on.
Gatekeepers at ports and rail yards use handheld devices to automatically capture and transmit more granular events like container pickup, drop-offs, mounting on chassis, and gate in/out times.
These tracking events get aggregated and analyzed in transportation management systems. As a result, everyone involved now has access to actionable data about what is happening with each container down to street turn-by-turn directions (and this knowledge can be used to tighten up and optimize logistics and, eventually, pass on the benefits to the end consumer).
AI and machine learning optimize logistics
With exponentially more data about container movements now available, AI algorithms can detect patterns and predict potential outcomes. Machine learning models are trained to forecast arrival times at ports, queue lengths, customs waits and just about everything else you can imagine.
By benchmarking against historical trends, abnormalities get flagged immediately so proactive measures can be taken to minimize delays. For example, if a container is sitting longer than usual at a port, the system automatically notifies the responsible parties to get it moving.
Recommendation engines access data from across the whole supply chain network to provide dynamic guidance to optimize routing and warehousing. The algorithms generate smarter stowage plans to load vessels and route containers in the most efficient sequence.
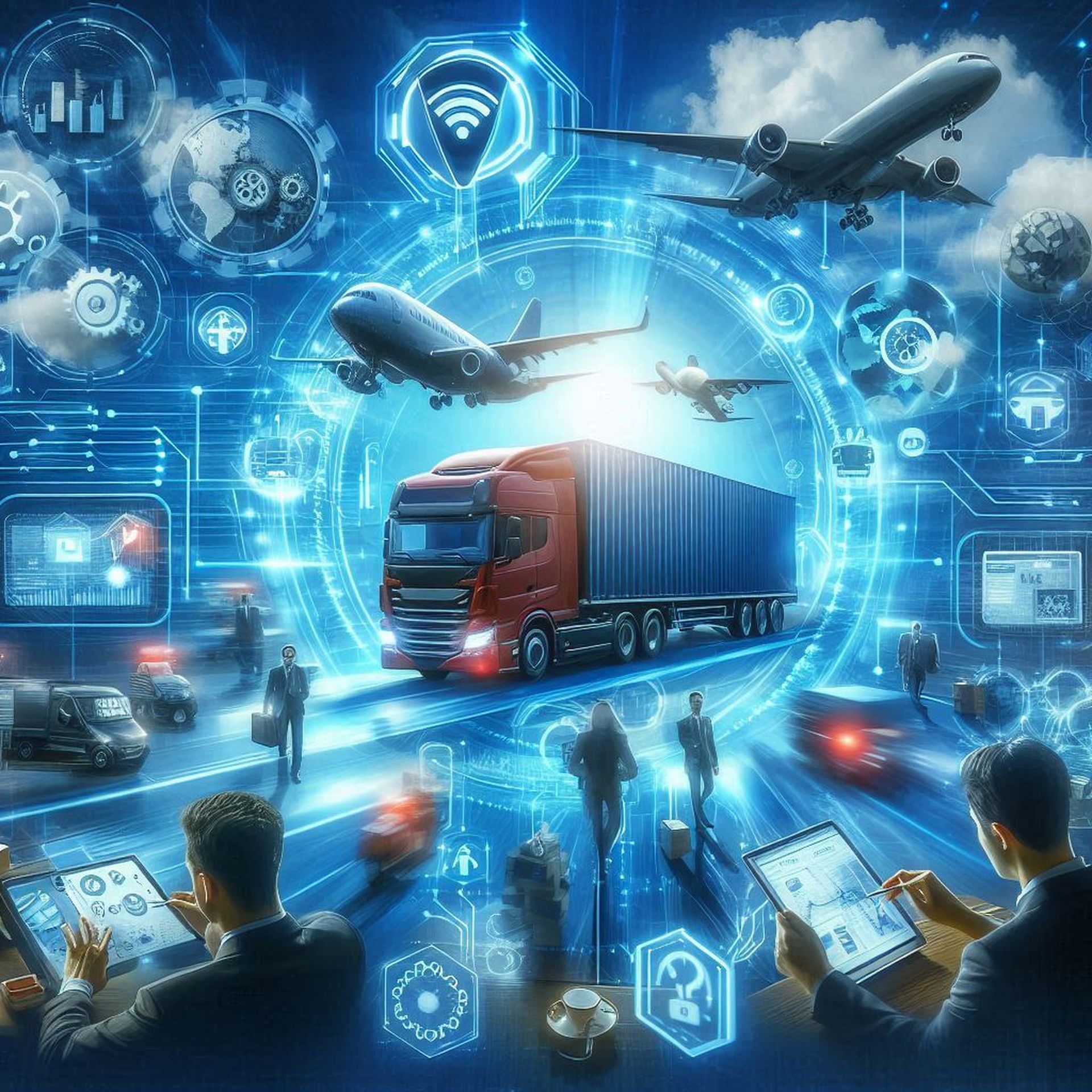
As conditions change, the systems rapidly recalculate plans and prescribe next best actions to ensure deliveries keep moving. Humans handle exceptions, while AI handles the day-to-day execution.
Orchestrating end-to-end logistics
Shipping companies are offering integrated control towers that combine real-time tracking data, weather and traffic reports, customs information, and booking statuses. These systems provide complete supply chain visibility and event management from factory to destination port. This is something that would have been thought to be impossible just a couple of decades back.
Control towers use workflows, alerts, and dashboards so customers can proactively monitor order status. Issues get flagged early with notifications sent to both shippers and consignees. From there, they can collaborate to resolve problems before there is downstream impact.
Using predictive analytics, the platform automatically makes recommendations on optimally routing orders across carrier networks. It might suggest moving some containers to trucks or rail to avoid delays from potential port congestion. This level of supply chain orchestration minimizes costs and provides better customer service – a win-win for everyone involved.
Benefits of next-gen logistics
This combination of sensors, machine learning, and collaborative systems are fundamentally improving efficiency, transparency, and resiliency of shipping in a big way. Some of the main benefits include:
- Real-time container tracking and status updates
- Reduced waiting times at ports, rail yards
- Just-in-time loading/unloading for vessels & trucks
- AI-optimized stowage planning on ships
- Predictive ETA calculations down to street level
- Exception management workflows to resolve issues
- Reduced costs through network optimization
Final word
The latest wave of technologies offer unmatched visibility into the end-to-end journey of shipping containers. Instead of managing logistics chaos, supply chain partners now collaborate with data-driven confidence and agility. Shipping goods across continents continues to get faster, cheaper, and more reliable.
While the shipping industry still faces headwinds from trade wars, labor shortages and economic turbulence, technology is providing the tools and insights needed to chart a steadier course towards growth and profitability.
Featured image credit: Freepik