In an increasingly digitized world, the Human Machine Interface (HMI) stands at the forefront of our interaction with technology. It is the bridge between humans and machines, encompassing the design and study of interfaces that are intuitive, user-friendly, and effective for a wide range of tasks.
In simple terms, an HMI is a user interface that allows humans to interact with machines. HMIs typically consist of a display device, such as a touchscreen or monitor, and input devices, such as push buttons, keyboards, and joysticks. The display device is used to show the user information about the machine or system, such as its status, operating parameters, and any alarms. The input devices are used to control the machine or system.
HMIs are used in a wide variety of industries, including manufacturing, food and beverage, power generation, and transportation. In manufacturing, HMIs are used to control production lines, monitor the quality of products, and troubleshoot problems.
But how does a Human Machine Interface work and how has it changed the industry we know? Let us explain.
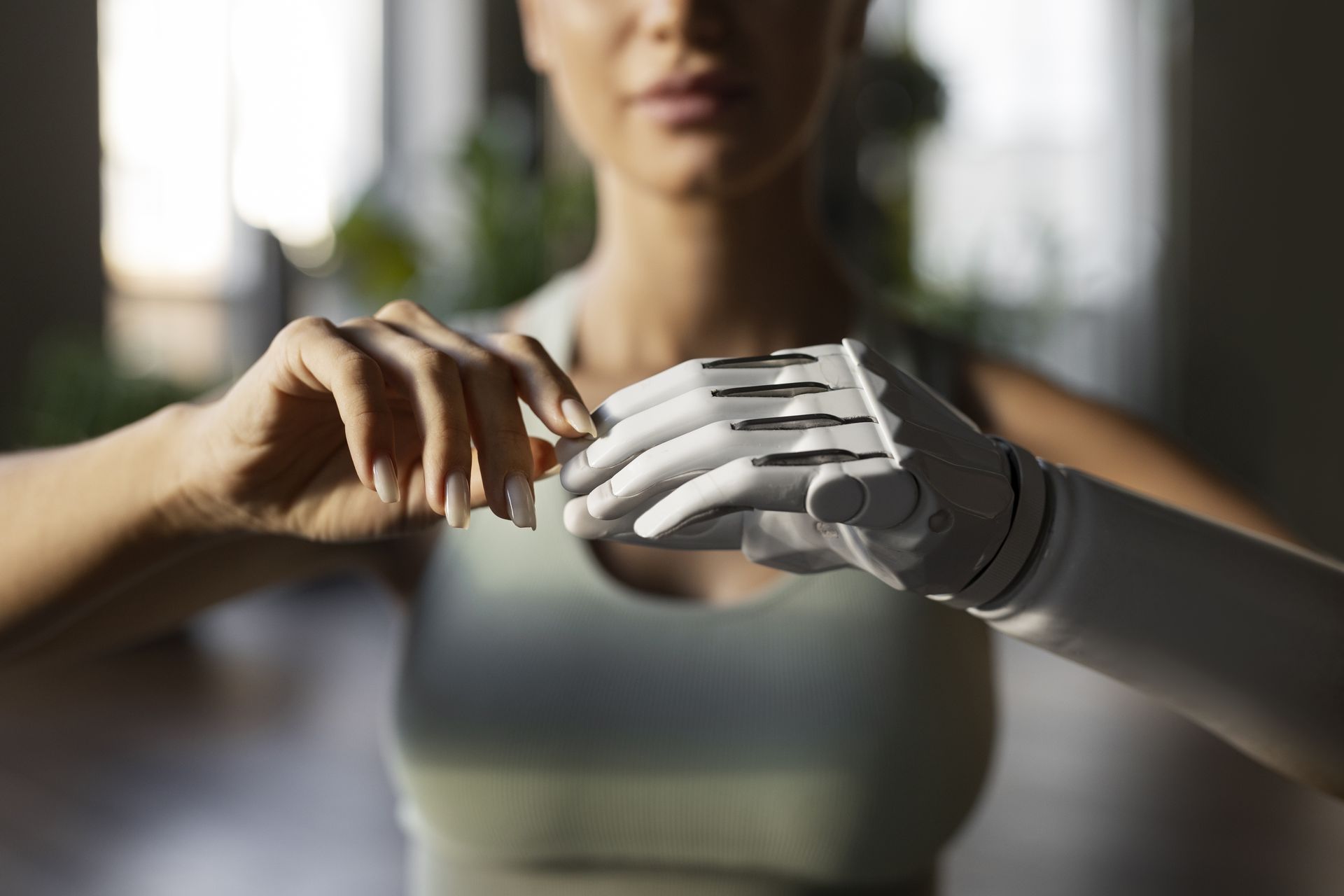
What is a Human Machine Interface?
A Human Machine Interface (HMI) is the study and design of the interaction between humans and machines, such as computers, software, and other forms of technology. It involves designing interfaces that are intuitive, easy to use, and effective for achieving specific tasks or goals.
Human Machine Interface is a multidisciplinary field that draws on knowledge and techniques from psychology, computer science, design, and engineering to create systems that are user-friendly and efficient. The goal of HMI is to make technology accessible and usable by people with diverse backgrounds, abilities, and needs.
The field of Human-Machine Interface (HMI) has come a long way since its inception in the 1970s. From the early command lines to the modern voice recognition technology, HMI has evolved significantly over the years.
Early beginnings
The concept of Human Machine Interface can be traced back to the 1970s when computer systems were primarily used by experts and professionals. The first HMI systems were based on command lines, which required users to type specific commands to interact with the computer. These systems were not user-friendly and were limited to a select few.
Graphical User Interfaces (GUIs)
The introduction of GUIs in the 1980s revolutionized the HMI landscape. GUIs use visual elements such as icons, windows, and menus to interact with the computer. This made computing more accessible to a wider audience, including non-technical users. The introduction of GUIs also led to the development of mouse technology, which further enhanced the user experience.
Web-based interfaces
The rise of the internet in the 1990s led to the development of web-based interfaces. These interfaces allowed users to access information and perform tasks online, without the need for a physical computer. This marked a significant shift in the way people interacted with technology and paved the way for the modern web-based interfaces we use today.
Voice recognition technology
The latest trend in Human Machine Interface is the integration of voice recognition technology. With the advent of virtual assistants such as Siri, Alexa, and Google Assistant, users can now interact with technology using voice commands. This technology has made computing more accessible and convenient, especially for people with disabilities.
Currently, there is a growing trend towards the use of artificial intelligence (AI) in Human Machine Interface. AI-powered interfaces are becoming more prevalent, and they are capable of learning and adapting to user behavior. This technology has the potential to create more personalized and intuitive interfaces, making computing more accessible and enjoyable for everyone.
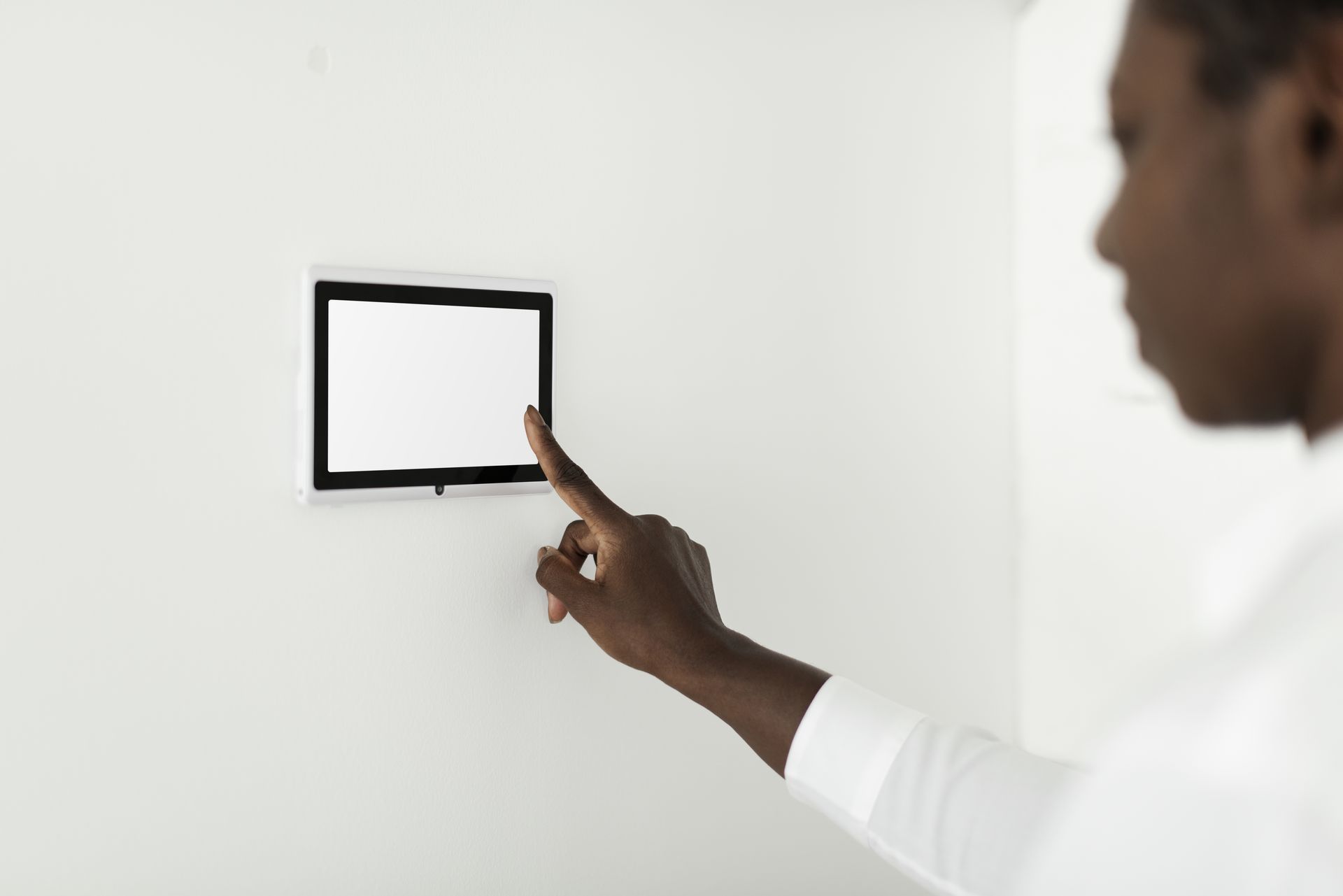
How does HMI work?
Human Machine Interfaces typically consist of a display device, such as a touchscreen or monitor, and input devices, such as push buttons, keyboards, and joysticks. The display device is used to show the operator information about the machine or system, such as its status, operating parameters, and any alarms. The input devices are used to control the machine or system.
HMIs are typically connected to a Programmable Logic Controller (PLC). A PLC is a computer that is used to control machines and systems. The PLC collects data from sensors and other input devices and then uses this data to control outputs, such as motors, valves, and actuators.
The Human Machine Interface communicates with the PLC over a communication network. This network can be wired or wireless. The Human Machine Interface sends commands to the PLC, and the PLC sends data back to the HMI.
AI in manufacturing: The future of Industry 4.0
The communication protocol used between the Human Machine Interface and the PLC depends on the specific HMI and PLC. Some common protocols include Ethernet/IP, Modbus, and Profibus.
The Human Machine Interface software is responsible for displaying the information from the PLC and for processing the user’s input. The HMI software also typically includes a number of features to help the operator, such as alarms, trends, and data logging.
Human Machine Interfaces can be programmed using a variety of software packages. Some Human Machine Interface software packages are proprietary, while others are open source.
Examples of HMIs are as follows:
- Touchscreen panels
- Monitor-based HMIs
- Panel PCsMobile HMIs
- Cloud-based HMIs
Touchscreen panels
Touchscreen panels are the most common type of Human Machine Interface. They are typically made of glass or plastic, and they have a touchscreen that allows the operator to interact with the HMI. Touchscreen panels are available in a variety of sizes, from small panels that can be installed in the palm of your hand to large panels that can be mounted on a wall.
Touchscreen panels are typically used in applications where the operator needs to be able to interact with the HMI quickly and easily. For example, touchscreen panels are often used in manufacturing applications to control machines and production lines.
Monitor-based HMIs
Monitor-based Human Machine Interfaces are similar to touchscreen panels, but they use a monitor instead of a touchscreen. Monitor-based HMIs are typically used in applications where the operator needs to see a lot of information at once. For example, monitor-based HMIs are often used in power generation plants to monitor the status of generators and other equipment.
Panel PCs
Panel PCs are a combination of a monitor and a computer. They are typically mounted in a panel and used to control machines and systems. Panel PCs are available in a variety of sizes and configurations.
Panel PCs are typically used in applications where the Human Machine Interface needs to be able to perform complex tasks, such as running data logging and analysis software.
For example, panel PCs are often used in food and beverage plants to control manufacturing processes.
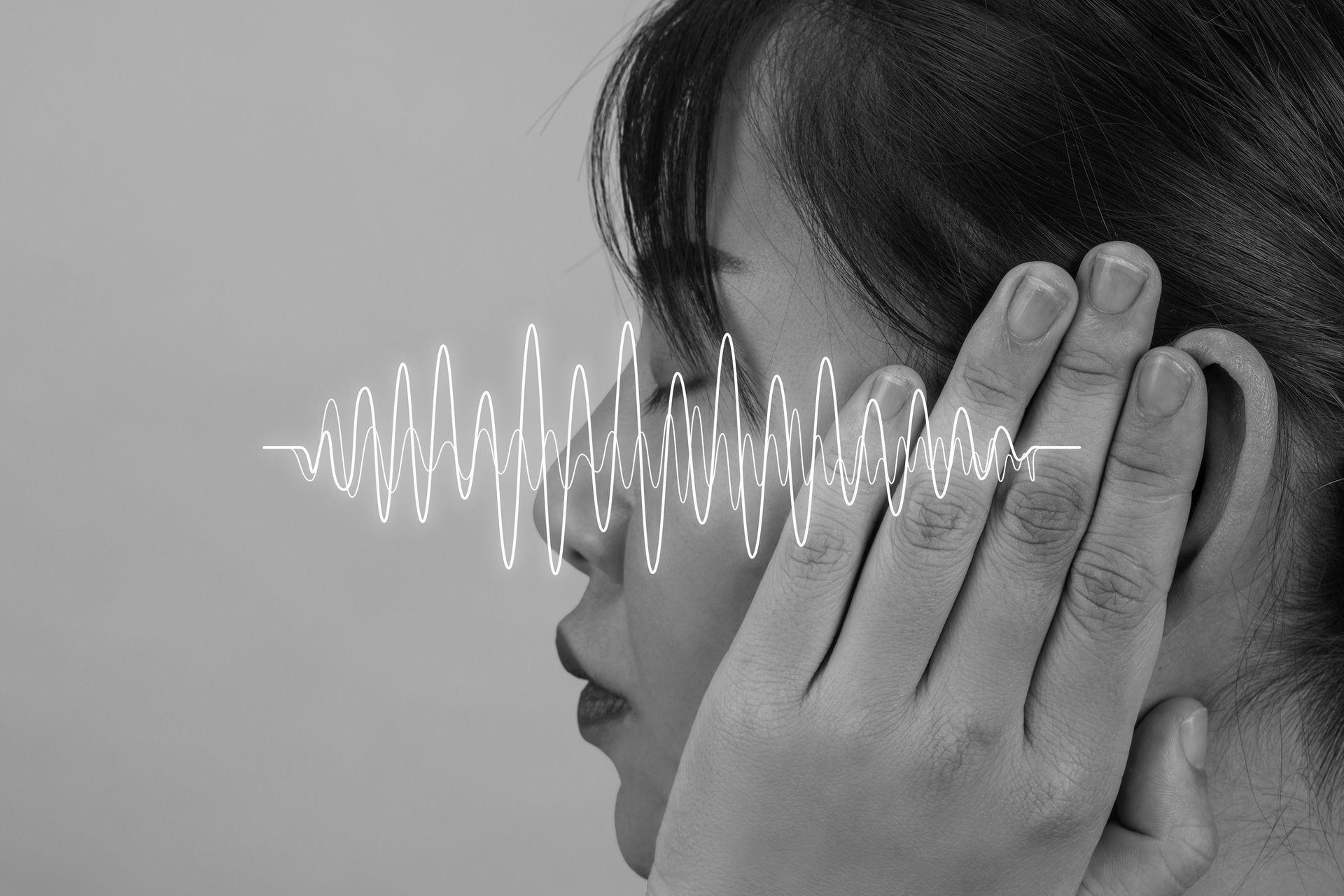
Mobile HMIs
Mobile Human Machine Interfaces are HMIs that can be used on mobile devices, such as smartphones and tablets. Mobile HMIs are typically used in applications where the operator needs to be able to monitor and control machines and systems from anywhere.
For example, mobile HMIs are often used in transportation applications to monitor and control the status of vehicles.
Cloud-based HMIs
Cloud-based Human Machine Interfaces are HMIs that are hosted in the cloud. This means that the HMI can be accessed from anywhere with an internet connection. Cloud-based HMIs are typically used in applications where the operator needs to be able to monitor and control machines and systems from multiple locations.
For example, cloud-based HMIs are often used in retail applications to monitor and control the status of stores.
A cornerstone for industrial systems
Human Machine Interfaces (HMIs) play a critical role in industrial control systems. They provide a way for operators to monitor and control machines and processes, and to troubleshoot problems.
As mentioned before, HMIs are typically connected to Programmable Logic Controllers (PLCs). PLCs are computers that are used to control machines and processes. HMIs communicate with PLCs over a communication network. This network can be wired or wireless.
HMIs typically have a display device, such as a touchscreen or monitor, and input devices, such as push buttons, keyboards, and joysticks. The display device is used to show the operator information about the machine or system, such as its status, operating parameters, and any alarms. The input devices are used to control the machine or system.
HMIs are used in a wide variety of industries, including manufacturing, food and beverage, power generation, and transportation.
Some specific examples of how HMIs are used in industry include:
- In a manufacturing plant, an HMI can be used to control a production line. The HMI can be used to start and stop the production line, to adjust the speed of the production line, and to monitor the quality of the products being produced
- In a power generation plant, an HMI can be used to monitor and control the status of generators and other equipment. The HMI can be used to start and stop generators, to adjust the output of generators, and to monitor the performance of generators
- In a transportation system, an HMI can be used to monitor and control the status of vehicles. The HMI can be used to track the location of vehicles, to monitor the condition of vehicles, and to control the operation of vehicles
HMIs play an important role in industrial control systems by providing a way for operators to monitor and control machines and processes, and to troubleshoot problems. HMIs can help to improve productivity, quality control, safety, and maintenance.
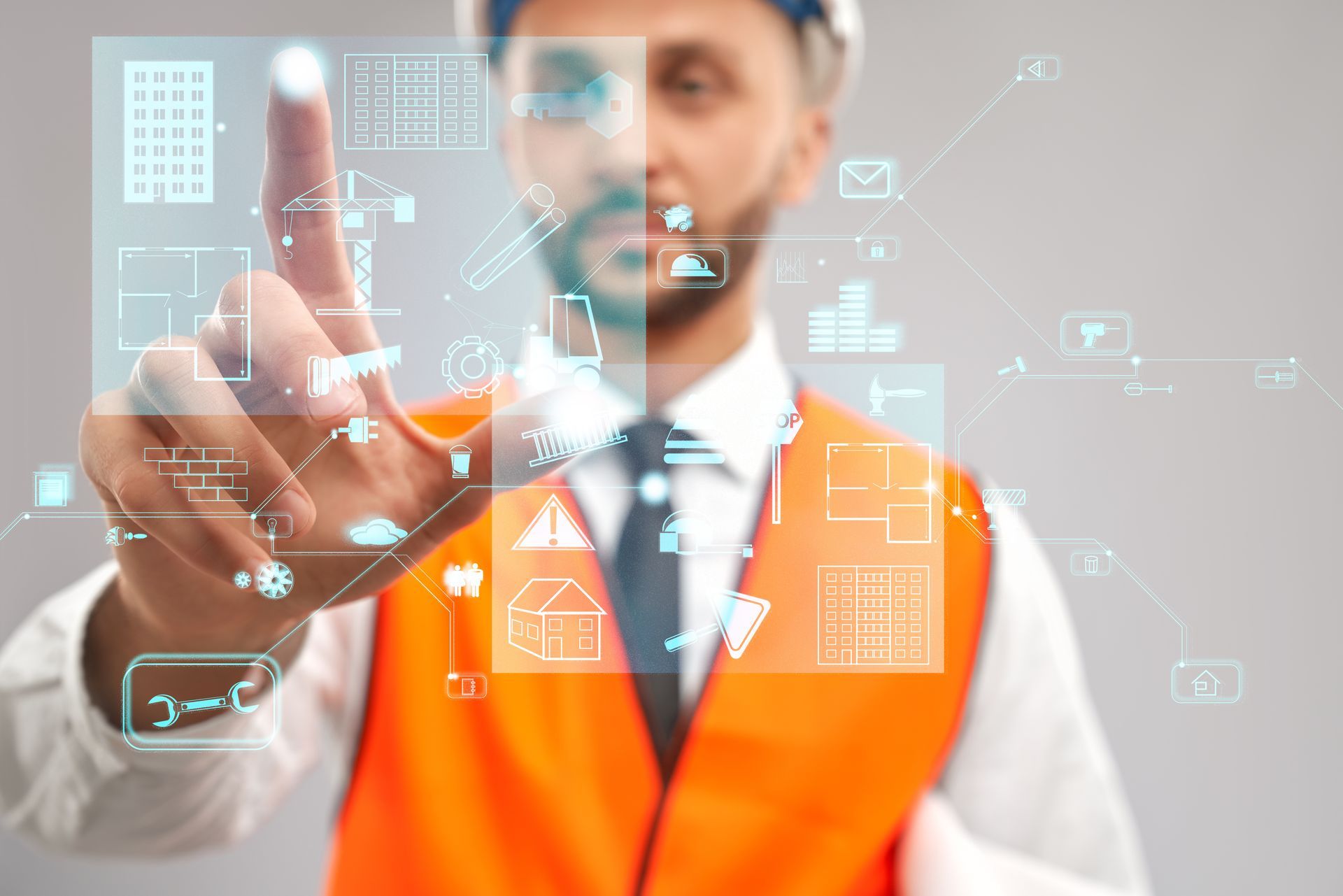
HMI vs SADA
Human Machine Interface (HMI) and Supervisory Control and Data Acquisition (SCADA) are both systems that are used to monitor and control industrial processes. However, there are some key differences between the two systems.
The main difference between HMI and SCADA is that HMI is used to monitor and control individual machines and systems, while SCADA is used to monitor and control large and complex industrial processes.
Another difference between HMI and SCADA is that HMI is typically used by operators who are located near the machines or systems that they are controlling, while SCADA can be used by operators who are located remotely from the machines or systems that they are controlling.
Finally, HMI systems are typically smaller and simpler than SCADA systems. HMI systems are typically used for single-user applications, while SCADA systems are typically used for multi-user applications.
Featured image credit: rawpixel.com/Freepik.