A new machine learning framework developed at the U.S. Department of Energy’s Brookhaven National Laboratory can hone in on which parts of a multistep chemical conversion should be altered to increase productivity. The technique may assist researchers in determining the shape of catalysts, also known as chemical dealmakers that speed up reactions.
Machine learning framework is used to increase productivity
The method to examine the carbon monoxide (CO) to methanol conversion using a copper-based catalyst was devised by the team. The reaction has seven simple elementary procedures.
“Our goal was to identify which elementary step in the reaction network or which subset of steps controls the catalytic activity,” said Wenjie Liao, one of the study’s authors, who is a Stony Brook University graduate student involved with Brookhaven Lab’s Chemistry Division’s Catalysis Reactivity and Structure (CRS) group. The paper is published in the Catalysis Science & Technology journal.
“We used this reaction as an example of our ML framework method, but you can put any reaction into this framework in general,” said Ping Liu, the leader at the CRS team.
Consider a rollercoaster with lots of different-sized hills. The height of each peak reflects the energy needed to go from one step to the next. Catalysts reduce “activation barriers” by making it simpler for reactants to combine or allowing them to do so at lower temperatures and pressures. A catalyst must target the step or steps that have the most influence in order for the reaction to move forward more quickly.
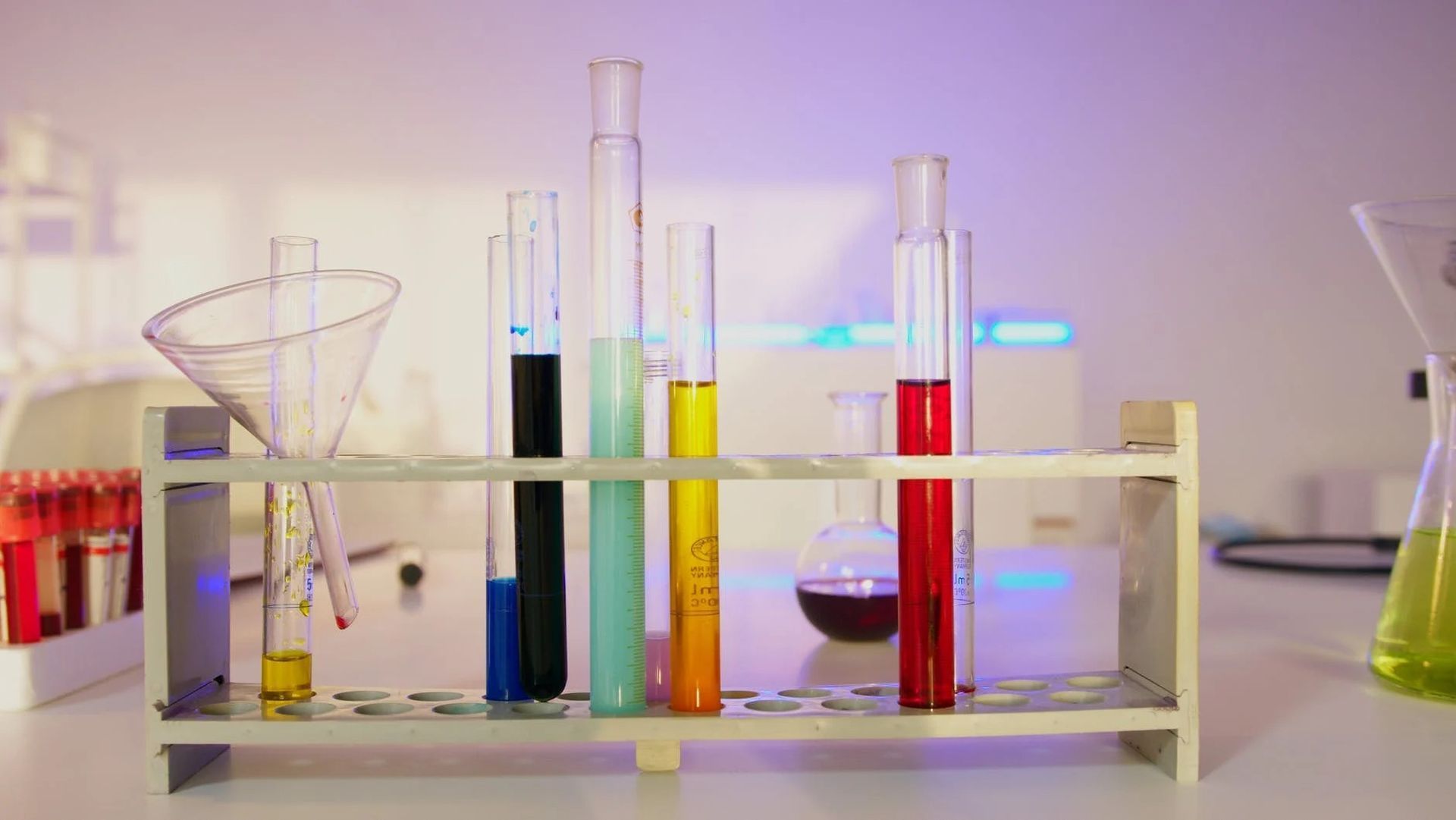
Traditionally, scientists attempting to improve a reaction have tried to figure out how varying one activation barrier at a time might affect the overall yield. This form of inquiry may reveal which stage is “rate-limiting” and which steps determine reactant selectivity, that is, whether the reactants proceed to the intended product or down an alternative route toward an unwanted by-product.
“These estimations end up being very rough with a lot of errors for some groups of catalysts. That has really hurt for catalyst design and screening, which is what we are trying to do,” Liu explained.
The team is attempting to improve these estimations by developing a new machine learning framework that will allow chemists to predict how catalysis would impact reaction processes and chemical output more accurately.
“Now, instead of moving one barrier at a time we are moving all the barriers simultaneously. And we use machine learning framework to interpret that dataset,” said Liao.
The researchers said that this approach, in which reactivity is inferred from the structure of a product rather than its activity or chemical makeup, provides considerably more trustworthy outcomes, including how components in a reaction interact.
“Under reaction conditions, these steps are not isolated or separated from each other; they are all connected. If you just do one step at a time, you miss a lot of information — the interactions among the elementary steps. That’s what’s been captured in this development,” said Liu.
How the ML framework has been built?
The researchers began by preparing a data set to train their machine learning framework. The activation energy needed to convert one arrangement of atoms to the next through the seven steps of the reaction was modeled using DFT (density functional theory) calculations. Then the researchers conducted computer modeling to evaluate what would happen if they adjusted all seven activation barriers at once. Chemistry isn’t the only field of science that benefits from machine learning, if you want to learn more about quantum machine learning, we have an article for you.
“The range of data we included was based on previous experience with these reactions and this catalytic system, within the interesting range of variation that is likely to give you better performance,” explained Liu.
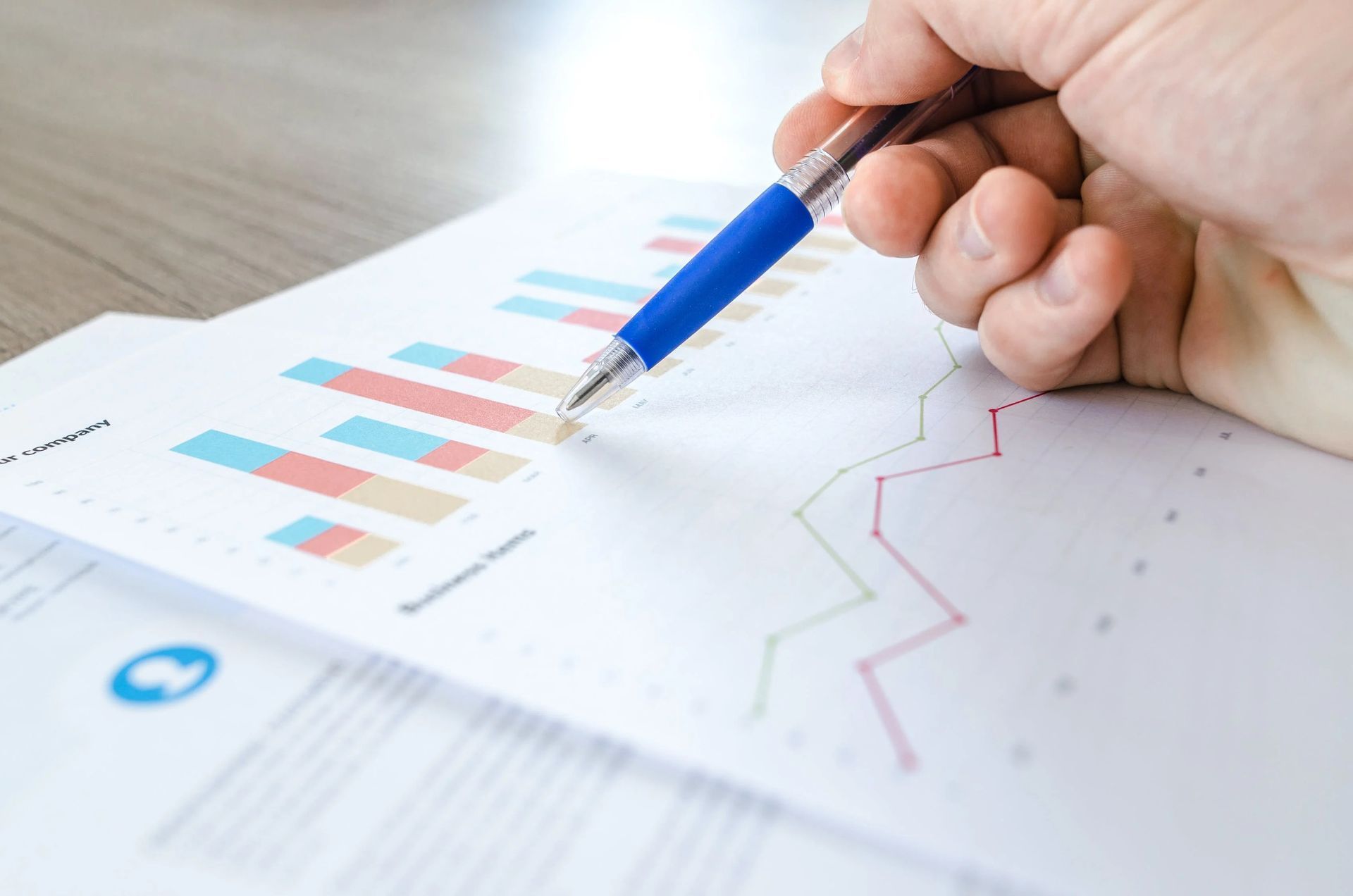
The researchers used a model to simulate variations in 28 “descriptors,” including the activation energies for the seven steps as well as pairs of steps changing two at a time, resulting in a comprehensive data set of 500 points. This dataset predicted how all those individual changes and pairs of changes would influence methanol production. The model then assessed each descriptor based on its relevance in determining methanol output.
“Our model ‘learned’ from the data and identified six key descriptors that it predicts would have the most impact on production,” said Liao.
After the most essential words had been identified, the researchers retrained the machine learning framework with just those six “active” criteria. This enhanced machine learning framework was able to predict catalysis activity solely based on DFT calculations for those six variables.
“Rather than you having to calculate the whole 28 descriptors, now you can calculate with only the six descriptors and get the methanol conversion rates you are interested in,” explained Liu.
According to the team, they can also apply the model to screen catalysts. The model predicts a maximum methanol production rate if they can produce a catalyst that improves the value of the six active identifiers.
The researchers compared the model’s predictions with the catalyst’s real-world performance and alloys of various metals with copper, finding that they matched up. The machine learning framework’s comparisons to previous methods for predicting alloy performance demonstrated that it was far superior.
The findings also illuminated how shifts in energy hurdles might impact the reaction mechanism. The data revealed how various steps within the process operate together, especially that lowering the energy barrier in rate-limiting step alone would not always improve methanol production if done alone. However, changing the energy barrier of a prior reaction network step while maintaining the rate-limiting step’s activation energy within an acceptable range would boost methanol yield.
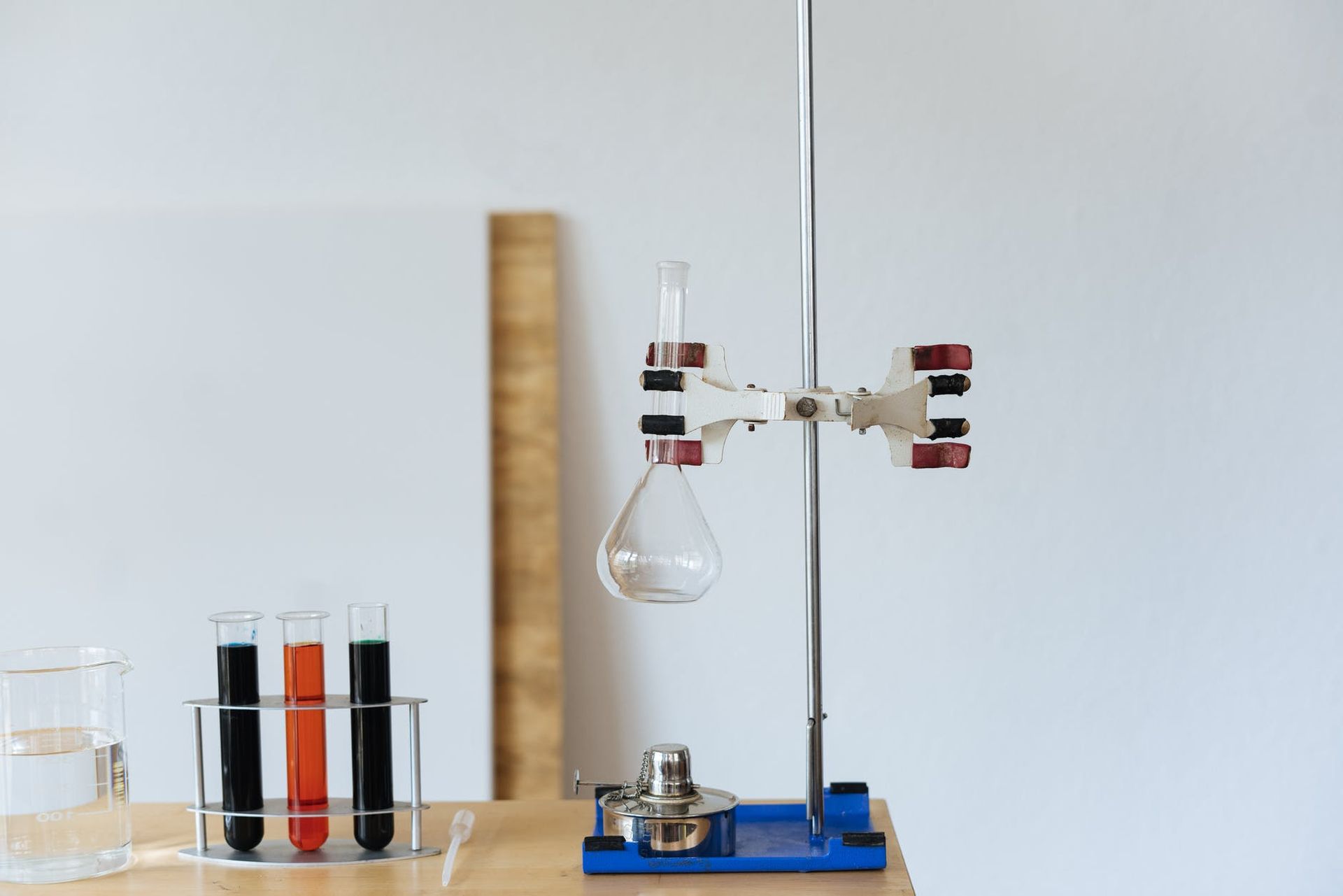
“Our method gives us detailed information we might be able to use to design a catalyst that coordinates the interaction between these two steps well,” explained Liu.
With data-driven machine learning frameworks, Liu is most intrigued by the potential to apply such techniques to more complicated reactions.
“We used the methanol reaction to demonstrate our method. But the way that it generates the database and how we train the machine learning framework and how we interpolate the role of each descriptor’s function to determine the overall weight in terms of their importance — that can be applied to other reactions easily,” said Liu.
The study was made possible by a grant from the Department of Energy Office of Science (BES). The calculations were done with computational resources at the Center for Functional Nanomaterials (CFN), a DOE Office of Science User Facility at Brookhaven Lab, and the National Energy Research Scientific Computing Center (NERSC), a DOE Office of Science User Facility at Lawrence Berkeley National Laboratory.
By the way, if you are interesed in ML methods, you can check out the history of machine learning, it dates back to the 17th century.